Urządzenia do znakowania daty nanoszą różne informacje o dacie na produktach, opakowaniach i etykietach. Znakowanie daty na produktach — zwłaszcza na produktach spożywczych, napojach i produktach farmaceutycznych — jest wymagane przez lokalne przepisy na całym świecie. Producenci potrzebują również znaków systemowych, takich jak kody produkcyjne, do własnego wewnętrznego śledzenia oraz do zapewnienia szybkiej dostawy produktów na rynek. Data wytworzenia produktu określa również jego datę ważności, która musi być umieszczona w widocznym miejscu na żywności, napojach i produktach farmaceutycznych oraz na ich opakowaniach.
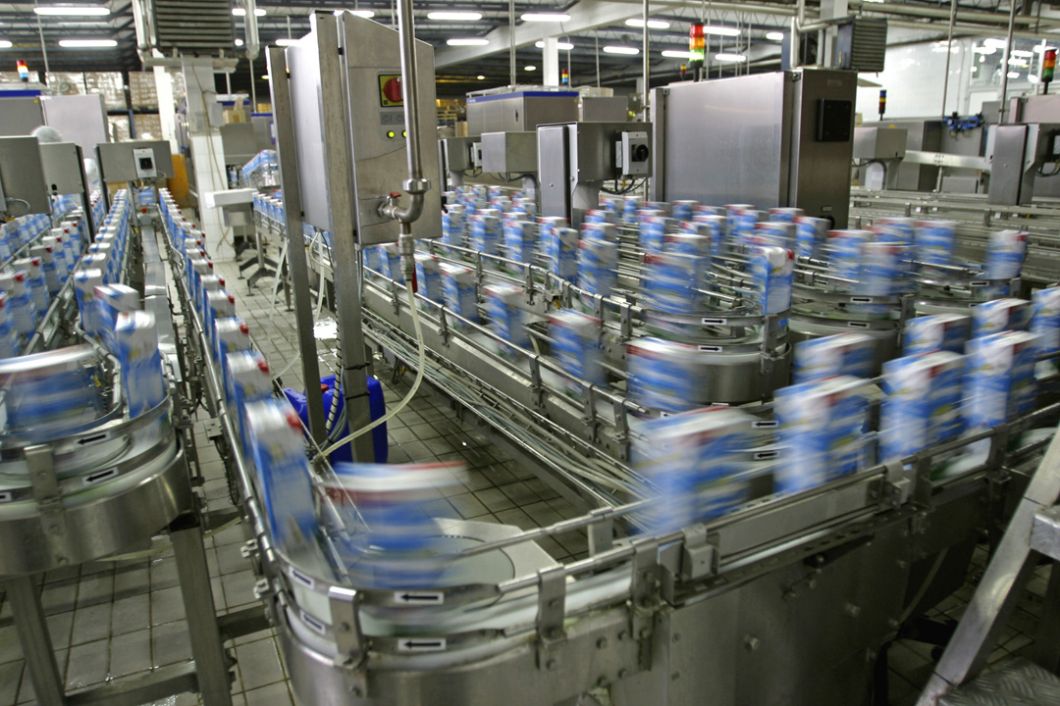
Jakim urządzeniem znakować na produktach
Często urządzenia do znakowania daty, które są używane do małych ilości produktów, służą do nanoszenia kodów ręcznie. Większość urządzeń do znakowania daty jest obecnie używana na liniach produkcyjnych o dużej prędkości, na których kody są nanoszone z prędkością linii produkcyjnej, co wymaga, aby system znakowania był w stanie utrzymać wysoką jakość druku podczas drukowania na przemieszczających się produktach i opakowaniach. W przypadku niektórych z tych urządzeń znakujących na linii produkcyjnej operatorzy linii ręcznie generują kody na początku zmiany roboczej każdego dnia. Większość dzisiejszych urządzeń do znakowania daty jest skomputeryzowana i zawiera oprogramowanie do automatycznego generowania i nanoszenia kodów daty na duże ilości produktów.
Jakie technologie wykorzystuje się do znakowania daty
Urządzenia do znakowania daty mogą korzystać z różnych technologii drukowania. Mogą one wykorzystywać technologię ciągłego druku atramentowego, termicznego druku atramentowego lub znakowania laserowego do nanoszenia kodów na produkty, a także systemy drukowania i aplikowania etykiet. Na przykład drukarki termotransferowe są często montowane na etykieciarkach na liniach produkcyjnych w celu drukowania informacji zmiennych, w tym kodów daty, bezpośrednio na etykiecie tuż przed naklejeniem jej na produkty przemieszczające się na linii pakującej.
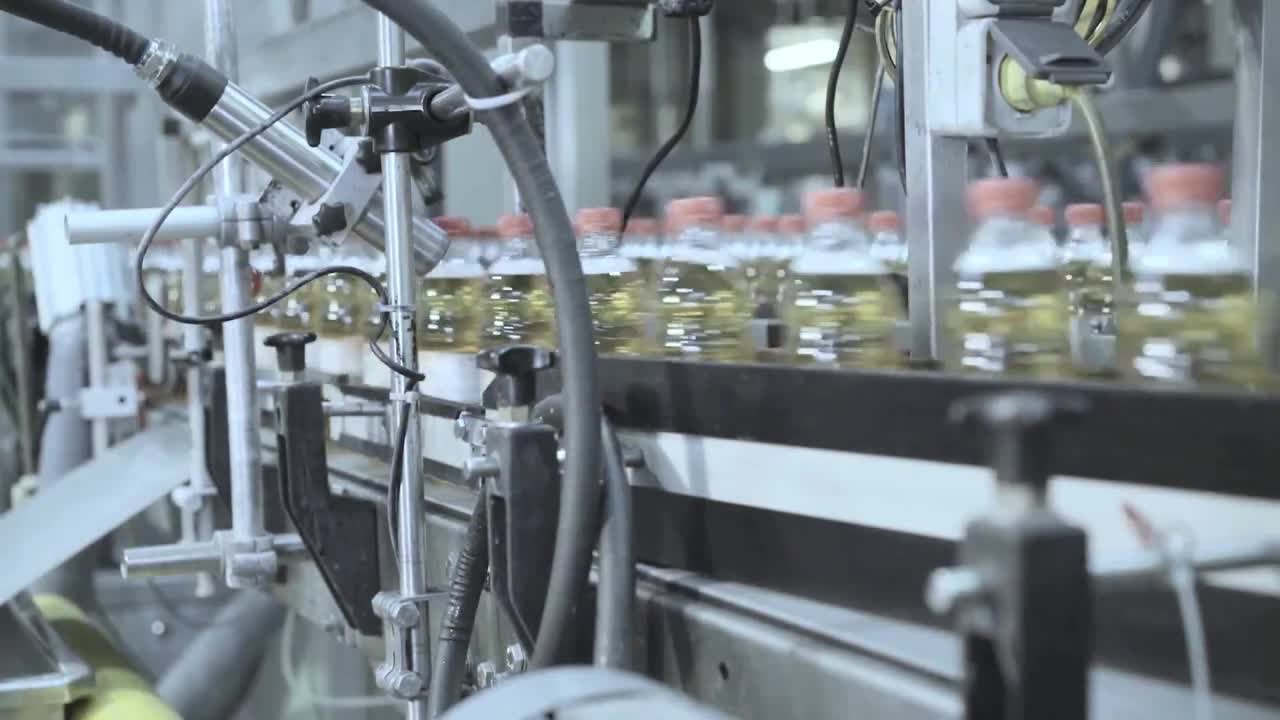
Na czym polega druk atramentowy przemysłowy?
W systemach druku atramentowego strumień atramentu przechodzi przez dyszę w głowicy drukującej. Rezonator piezoelektryczny wibruje, rozbijając strumień atramentu na jednakowe, pojedyncze krople. Elektroda ładowania jest przymocowana w pobliżu punktu rozpadu atramentu. Wielkość każdej kropli, która odrywa się od strumienia, jest proporcjonalna do przyłożonego napięcia. Naładowane krople przechodzą następnie pomiędzy dwiema przegrodami, pomiędzy którymi przepływa wysokie, stałe napięcie. Dzięki temu krople atramentu docierają do podłoża w dokładnie określonym miejscu, aby uzupełnić drukowany kod i zapewnić jego czytelność.
Polecany model drukarki: Videojet 1880
Jak działa drukarka termiczna?
Wkłady lub głowice drukujące termicznych drukarek atramentowych wystrzeliwują ku przesuwającym się opakowaniom strumień maleńkich kropelek atramentu. Błyskawiczne przełączanie umieszczonych pod nimi elementów oporowych sprawia, że każda z precyzyjnie skalibrowanych, umieszczonych w jednym lub wielu rzędach dysz wyrzuca z siebie drobiny atramentu. Te elementy oporowe powodują wrzenie niewielkich ilości atramentu. Termiczny druk atramentowy jest z natury czysty, a głowice drukujące są stosunkowo małe, co pomaga w integracji z liniami pakującymi o ograniczonej przestrzeni. Możliwe jest uzyskanie czasu schnięcia krótszego niż jedna sekunda, co przyspiesza produkcję i zmniejsza ryzyko zamazania lub nieczytelności kodów.
Polecany model drukarki : Videojet 8520
Jak działają drukarki laserowe w przemyśle znakowania produktów?
Inaczej wygląda to w przypadku drukarek laserowych, gdzie wiązka światła pozostawia ślad na wierzchniej warstwie podłoża lub fizycznie ją modyfikuje. Wiązka światła systemu kodującego jest kierowana przez dwa lustrzane galwanometry, które ustawiają wiązkę lasera w dwóch płaszczyznach, tworząc kod daty na powierzchni produktu lub opakowania.
Polecany model drukarki : Videojet 3350
Na czym polega druk termotransferowy?
Systemy druku i nanoszenia termotransferowego wykorzystują drukarkę termotransferową, która drukuje z taśmy, przenosząc znaki z taśmy na powierzchnię etykiety, po czym etykieta jest naklejana na przemieszczający się produkt lub opakowanie. W tym procesie można osiągnąć szybkość etykietowania do 1000 elementów na minutę.
Polecany model drukarki : Videojet DataFlex 6530 & 6330
Videojet 3350
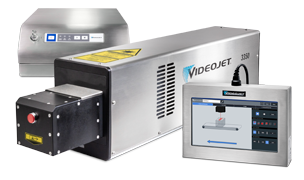
Videojet 1880 +

Videojet DataFlex 6530
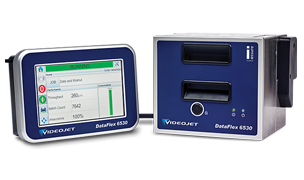
Podsumowanie
Aby określić, która z tych technologii jest najlepsza dla danej linii produkcyjnej, firmy muszą wziąć pod uwagę różne czynniki, w tym podłoże, na którym będą drukowane kody, prędkość linii produkcyjnej, stabilność obsługi produktów i opakowań na linii, dostępność miejsca do zainstalowania drukarki kodów oraz koszty zakupu i eksploatacji.
Kategorie
- Maszyny do Pakowania
- Maszyny do Napełniania Butelek
- Kartoniarki
- Maszyny Wytłaczające
- Systemy Pakowania Produktów Elastycznych
- Opakowania do Żywności
- Maszyny Formujące
- Urządzenia do znakowania laserowego
- Znakowanie Produktów
- Etykietowanie produktów
- Linie Produkcyjne
- Śledzenie i identyfikacja produktu
- Zgrzewarki Próżniowe
- Drukowanie Danych Zmiennych